|
Sony Videoflight Facilities,
History and Equipment
Sony - Sponsors and demonstrates the world's smallest
and lightest videotape recorder (model PV-100), designed for the
technological, industrial, educational, medical, sports and arts markets. Used
two inch open reel tape in a 2 head helical scan system. The PV100 was
adopted by American Airlines in 1964 for in-flight movies. Ampex was to
sue Sony over this in 1966.
|
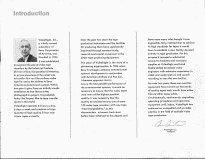 |
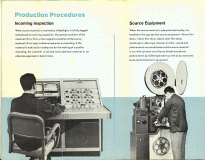 |
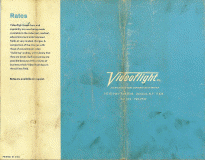 |
Introduction
Videoflight, Inc., a wholly owned subsidiary of Sony Corporation of
America, was founded in 1964. It was established to augment the sale of
video tape recorders by the Industrial Products Division of Sony
Corporation of America. Its primary business at the outset was to transfer
first run films to Sony video tape for use by the airlines in Sony
airborne entertainment systems. Within one year it grew from an initially
simple installation to that shown in the photograph on page 2. It is
probably today the largest film-to-tape transfer center in the world.
Videoflight operates 24 hours a day, 6 days a week and produces a large
quantity of high quality 2-hour and 4-hour tapes a
month.
Over the past two years the tape production techniques and the
facilities for producing them have significantly improved through constant
study, research and capital investment in the latest tape producing
equipment.
The story of Videoflight is the story of a pioneering organization. In
1964 when Sony first began airborne entertainment systems' development in
conjunction with American Airlines and Pan Am, it
became apparent that to assure the best possible
performance of the entertainment systems, it would be necessary to ensure
that the video tapes used were of the highest possible quality. It was
necessary that this quality be realized on anyone of some 150 video tape
recorders with any tape. "Interchangeability," as this
characteristic is known, had never before been achieved to this degree and
there were many who thought it was impossible. Sony
realized that to achieve its high standards for tapes it would have to
establish a new facility devoted entirely to tape production. For this
purpose it invested a substantial amount in facilities and necessary
supplies at Videoflight and hired highly skilled
broadcast video engineers with extensive experience in video and audio
(picture and sound) recording to man the new facility.
For over two years these men and this equipment have turned out
thousands of quality tapes each month from either films or other tapes
while, simultaneously, continuously upgrading operating procedures and
operating equipment until, today, Videoflight has achieved an unequalled
and enviable position in the field of multiple video tape production.
|
Tape Duplication
The management of Videoflight recognizes that there is now developing a
vast demand for multiple copies of tape in such fields as medical
education, sales training, cable television, industrial communication,
home entertainment and general education. To meet this demand Videoflight
has recently added equipment to permit the production of video tapes in
any configuration and to any standard. For example, multiple tapes may now
be made for the Sony EV-200, industrial Videocorder, the Sony CV-2000
series Home Videocorders, in addition to the Sony PV-120A, PV-120Al,
PV-120U and video tape recorders of other
manufacture.
Special Requirements Where the source material is film and it is
available to Videoflight for a very limited time (as happens with
pre-release films) Videoflight combines the capabilities of its film
chains and Allenized broadcast VTR to make master video tapes from which
multiple copies may be made in the appropriate configuration (that is,
1/2, 1 or 2 inch video tape.)
Videoflight has acquired extensive experience in making tapes from
Cinemascope-type films. The necessary change in
aspect ratio is achieved by skilled operation of the electronic
controls in theVideoflight system while following the script from which
the film was made. The essential portions of each
scene are recorded for later reproduction.
The Videoflight color film chain provides red, blue and green color
output signals which may be encoded appropriately to
permit recording on video tape.
For example, excellent line sequential color
recordings have been made at Videoflight on the Sony PV-series
Videocorders. SECAM and other recording systems may also be used.
|
Production Procedures
Incoming Inspection
When source material is received by Videoflight, it is fully logged and
passed to incoming inspection. The optical condition of the material (if
it is film) or the magnetic condition of the source material (if it is
tape) is determined prior to recording. If the material is technically
inadequate for the making of a quality recording,
the customer is advised and substitute material or an alternate approach
is determined.
Source Equipment
When the source material is adequate technically, it is loaded on the
appropriate source equipment-35mm film chain, 16mm
film chain, 35mm color film chain, quadruplex video tape recorder or
other-sound and picture levels are established and the source material is
run with constant surveillance of both sound and picture
levels by skilled operators as well as by automatic level-control
electronic equipment.
Playback and Quality Control
When the recording is completed it is played back on the recording
machine, as well as on other similar machines to assure good audio and
video quality and interchangeability. If anyone of these elements falls
below professional standards or if any other defect appears (such
as tape drop-out), the tape is rejected by the operator and a complete
re-run is performed. If the tape reaches the established quality. standard
as far as the operator is concerned, it is passed on
to the Quality Control Department where it is again put through rigorous
tests.
If it passes those tests it goes to the Shipping Department where its
serial number, the addresses and the subject matter are noted. Logging of
the total number of transfers made, whether shipped
or not, and their dispositions are made accurately so that copyright
owners can be assured that no unauthorized showings
of the source material will be made.
Re-Use of Tapes
When tapes are returned for re-use, they are inspected for wrinkles or
other defects, spliced if necessary, and bulk-erased before transferring
new programs to them. Accurate records of tape erasures are also kept.
|
Rates
Videoflight know-how and capability are now being
made available to the industrial, medical, educational
and entertainment fields at very modest charges. A comparison of the
charges with those of conventional video "dubbing" studios, will
indicate that they are lower. Such economies are possible because of the
volume of business which Videoflight does in the
airlines field. ,
Rates are available on request.
This Brochure is in the Video Technology Reference
Section At SMECC
Although it is undated it came in with a group of
CV-2000 brochures form 1967. it seems to be in that time frame also
or perhaps a year earlier. - eas |
|
 |
Sony was the
first Japanese company to produce an Ampex-type VTR. Ibuka, who
believed that Sony's calling was making products for home use,
however, was not satisfied with the distinction. He thus directed
Kihara and his video development staff to research the use of
transistors to create a more compact VTR. In November 1959, they
succeeded in producing the first transistorized Ampex-style VTR,
which was a big step toward a smaller VTR.
Then in 1960
Sony and Ampex agreed to share their VTR know-how. Ampex was
anxious to gain Sony's knowledge in transistor application
technology. Sony, on the other hand, could learn about VTR
technology from Ampex. Masahiko Morizono, who had worked on audio
equipment at the Sony audio factory in Haneda, was enlisted to
help in this joint effort.
Unfortunately,
this project did not last long. There were limits to the Ampex
4-head VTR. When any of the rotary heads became work, it was
necessary to replace all of them, which was a major expense.
Kihara's staff developed a 2-head transistorized VTR in which the
individual heads could easily be replaced.
After research
and testing a total of five trial models using Ampex and Sony VTRs,
the end product was the world's first transistorized VTR, the
SV-201. This 2-head, helical scan type VTR with a tape speed of
seven inches/second (the same speed as an audio tape recorder) had
much better performance characteristics than any other VTR in the
market. Unfortunately, however, it was neither suited for
broadcasting nor home-use. With just 2 heads, the broadcasting
companies were not interested. It was also too large and expensive
for the average consumer. Sony decided to develop different
products for different markets. The result was Sony's PV-100. At
approximately one fiftieth the size of broadcast VTRs, it was
considered portable, and
represented a revolutionary breakthrough in miniaturization.
|
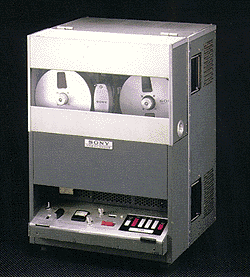 |
The PV-100 world's first and
smallest transistor VTR. |
|
Sony announced
the PV-100 in September 1962. Less than a year later, sales of the
2.48 million yen set began first in Japan, followed by export
sales to the United States. The PV-100 was intended for
business-use ie., industrial, educational, and medical
applications. Sony salespeople went from hospitals to schools and
airline companies selling the VTRs.
At the time,
most airlines used 8mm and 16mm films for their in-flight movies.
Flight attendants, however, found the film difficult to handle. It
often rolled off the reels or ripped. The short screening time
also made the whole process even more troublesome. Thus, the
airlines were very interested in Sony's suggestion of using VTRs
instead.
In 1964 and
1965, VTRs were introduced on American Airlines and Pan American
flights. Sony's job was to provide the software.
In order to deliver new tapes to the airlines on a weekly basis,
Sony established the In-flight
VTR Service, a VTR
duplicating factory in the suburbs of New York. This was seen as a
sure money-making venture.
However, flight
attendants seemingly did not treat tapes with much care. Flight
attendants would jam the open-reel tapes while threading them or
leave them near the beverage trays, where inevitably coffee would
spill over them. The original estimate that the tapes could be
used at least forty times was completely off target. Most tapes
came back in pitiful condition after just one use.
Despite these
troubles, Sony was relieved that the VTR, which was originally
considered marketable only to broadcasting companies, had come one
step closer to consumers. In addition, the basic technology behind
this VTR developed by Nobutoshi Kihara and Masahiko Morizono was
passed on to the 1-inch Omega VTRs and half-inch Betamax VTRs |
From the Sony History Site http://www.sony.net/Fun/SH/1-11/h1.html
|
PV-100:
First practical VTR developed in 1962 by Mr.
Kihara at Sony Corp. Spec's: Black and white, mono sound, two inch
tape, 5-3/4 IPS, 8"? reels, 120 minutes record / playback time,
25" x 17" x 17" (hwd), 145 pounds. Shown here, being
threaded by an American Airlines technician, for showing an in-flight
movie on 26 video monitors in various locations about the plane. The
in-flight models of the PV-100 had the record electronics removed to save
weight and power consumption. Passengers could also select an external
view through a video camera, located in the nose of the plane, during all
phases of their flight. Info & photo:
Electronics World Magazine - March, 1965
Courtesy Labguy's World www.labguysworld.com
|
|
|
|