|
Process and Machine Control and Other
Special Purpose Computers
by
O. K. LINDLEY
Sales Manager - Control and Simulation
Applications
Industrial Computer Section
The United States will be 200 years old in 1976. It will have
a population of somewhere around 216 millions. This population will demand
twice the goods and services available today. The work force will be only
about 30 per cent larger than it is today. This means that, using the same
production tools and methods we use today, the nation would be able to
produce only about 70 per cent of the goods and services in actual demand,
or - think of it! - a shortage of 76 billion man hours of labor in 1976.
Three possible solutions loom before us. First, and 11 1/2
hour day, that is, a 57 hour week for workers. Second, recruiting more
workers from among children, students, minor citizens, and housewives.
Third, increase by invention the individual output of workers.
We have only to look at these three choices to know the one we
have to make. We have to apply more and better machines to do more and
more of the work of the world. Then we have to apply machines to run
machines.
Some people get goose pimples when they contemplate this. The truth
of the matter is that what is happening to us now is hardly more than a
speeded-up continuation of a process that has been changing our methods of
production for 160 years.
When you boil it down to simplicity, we mean that we are now able to
harness power more efficiently than ever before. It means that we can
offset with sheer ingenuity the shrinking of our work force in proportion
to our population. As more machines run more machines, we can confidently
look forward to 1976, sure that we have nothing to fear in terms of
production - sure that the machine will shoulder still more of the ache
and burden of exhausting toil.
Here and now we have to look at MECHANIZATION and AUTOMATION.
Mechanization we already have to a high degree in certain industries. We
begin to get nearer to true automation when we come to a machine like the
Differential Analyzer which can present, immediately vital facts necessary
to certain engineering decisions. Design and control problems on
airplanes, for instance, can be analyzed by use of this kind of machine in
such a way that one engineer can find answers to them as quickly as twelve
engineers formerly.
We pass from that to true automation when a "brain" is
introduced into a machine to check and control it from within itself.
For example, a lathe is set to cut a certain bore. The bore
it cuts is immediately checked for size by an automatic operation which
brings a micrometer to the shaft. If the cut is not exact, an ad-
49.
|
ditional cut is automatically made. This cut
is again measured. The machine will not pass its own product until the
product meets minutely exact specifications. This is, so to speak,
"consciously self-controlled mechanical operation" and is true
automation.
Once such a machine is set in operation, however, it cannot be stopped,
in this sense: whatever model it turns out is fixed and increased
production of like model results. We can forecast, therefore, on the bas
is of increased production when, "true automation" comes, new
production processes will produce new products.
Computers, which were a novelty and available only at high cost a short
time ago, are now rapidly becoming practical and understandable tools of
industry. Already they have proved their worth in
scientific and engineering circles. In accounting and record keeping
they have been used mainly for routine work, but their use is being
extended to detail data processing and inventory work. In addition, highly
reliable computer components are being made available for process and
production control in factories.
During the period of computer growth and development those who have
known the story have been too busy to tell it effectively to industry. The
computer component manufacturers have done only a partial job of
merchandising their own products. It is not surprising therefore, to find
that specialists in the fields of motors, vacuum tubes, toasters,
television, power transformers, etc., are unfamiliar with the computer
field and with the opportunities it has to offer.
Let us view more computer products. The more you see and hear of
computers, the more adept you will be at applying this operational tool.
Original Network Analyzer - The first large computer built by General
Electric for the power and light companies to aid in their long tedious
calculations of power flow in their transmission lines. Today, 40 much
improved versions are in use throughout the world for power systems
studies and many common problems of vibrations and oscillating loads.
Matrix Rotator - A true knob twidler's paradise, the matrix rotator
provides the Army with a highly mathematical computer to evaluate tests
given to select Army personnel for the many jobs available.
Penalty Factor Computer - A large computer for solving problems in the
economic generation and distribution of electric power. It assists the
load dispatcher in the scheduling of power generation so that the cheapest
unit to deliver power to a load will be used in preference to a nearer but
more expensive unit to run.
Analog computers are useful, they save time and money and costly design
errors. Let us see why the use of analog computers has spread so widely
and examine the various types and their applications. The key to this
examination is the basic problem solving process itself.
50.
|
Consider the engineer about to start the
design of a product involving dynamic relationships, such as a paper mill
control, or a transformer, or a motor. He will have in mind the
performance specifications of the device, and some background knowledge on
how this sort of thing has been done In similar cases in the past. He will
then seek methods to jiggle the variables at his disposal,
such as components to be used, mass, damping, voltage, current and so
forth to obtain maximum results with minimum cost. The
"jiggling" may be done in various ways, inc1uding cut-and-try
methods, mathematical analysis and computations and the use of analog
computers. Let us contrast these methods and their cost.
The Cut-and-Try method was popular in the days of craftsmanship.
Several models of a design might have been built and tested and the best
adopted for production. While this ma, still be possible with an electric
toaster (though not economical), it is hardly feasible with a large
alternator. Besides, there is no way of assuring an optimum design.
Mathematical analysis usually allows us to describe the performance of
a device to be built in a way that is subject to numerical evaluation.
Optimum designs may be derived and a systematic design procedure results.
In many cases, however, the labor of evaluating the mathematical
description numerically is prohibitive for hand calculation. Digital
computers may be employed, and with their aid, this method of analysis
becomes practical. The digital computer is extremely accurate and
versatile for this purpose, although the labor of programming a problem
may be considerable, and the "feel" for the physica1 problem may
well be lost by the investigator. Also, as a generalization, the analog
computer approach will require less capital equipment by a factor of ten
or more. We can distinguish two methods for using these analog computers;
first is the use of the computer to evaluate the equations numerically,
taking advantage of the convenience, flexibility and speed 0f the analog
computer. The second approach consists of direct realization of the
problem from its physical description, without the intervening
mathematical analysis. This is made possible by the direct analogies which
may be drawn between physical arrangements, such as mass-spring systems,
and their computer equivalents. When you delve a little into the various
classes of analog computers, you will see the nature of this similarity,
and the manner in which it allows specific or cut-and-try solutions on the
computer model. The old method of cut-and-try has thus been made
economical by eliminating the construction of a separate sample for each
solution to the basic problems. Minimum cost solutions may then be arrived
at, because changes can be made rapidly and at a very low cost per change.
Now let us look at analog computers as they apply to simulation. All of
you, I am sure, recall the story of Aladdin and his wonderful magic lamp.
When he rubbed the lamp, he released a Genie who did his
every bidding. Today's modern engineer, Like Aladdin, also has a
magic lamp - this time in the guise of a computing mechanism. When he rubs
it properly, he can create for test purposes, unobtainable or non-existent
equipment. Furthermore, he can test and revise his theories before any
prototype equipment is designed, built, shipped, or installed.
51.
|
Power Control Simulator Computer - a
large special purpose computer for duplicating a jet engine for the
testing of auxiliary control s . An add it ional tool in the development
of controls for jet engines, the Simulator is designed to imitate an
actual engine so that real engine controls for any engine can be connected
directly to it. Both steady-state and transient operation are simulated
for all altitudes and flight conditions.
The use of computers as a simulator is well known in the field of steel
mill design and jet engine design. Some other applications are the
simulation of hydro-electric installations consisting of prime movers,
hydraulic transmissions, and generators. Simulators have also been built
in the field of electric motors, transformers, and air frame control
design. Another coming application of simulators will be in the reactor control
design field and the missile and rocket design areas.
Here are the principal reasons for using simulators:
1. Save time and money
2. Avoid expending valuable equipment in test 3. Provide for inclusion
of the human element in engineering studies
4. Substitute for unavailable apparatus
5. Provide a physical picture of the analyst's equations
By no means complete, this listing is intended as thought stimulation
for business-minded managers who are looking for ways to invest in order
to get better engineering results.
Now let us take a look at what we term MACHINES THAT RUN MACHINES. Our
current example is Numerical Machine Tool Control Systems. Beginning in
1948, the General Electric Company has pioneered in the development of
automatic control systems for machine tool applications. These systems
have fallen roughly into three categories:
1. Position controls (point-to-point)
2. Continuous position controls (velocity controls) 3. Process control
These machines have been developed to capitalize on three of
the basic motivations for automatic machine tools:
1. Increased productivity
2. Elimination of waste
3. Reduced set-up time and expense
Current thinking and development wort is being devoted to enhance these
three characteristics as well as to include some further benefits of
automatic machine tools. These devices should also:
1. Optimize the transfer of information from designer to machinist
52
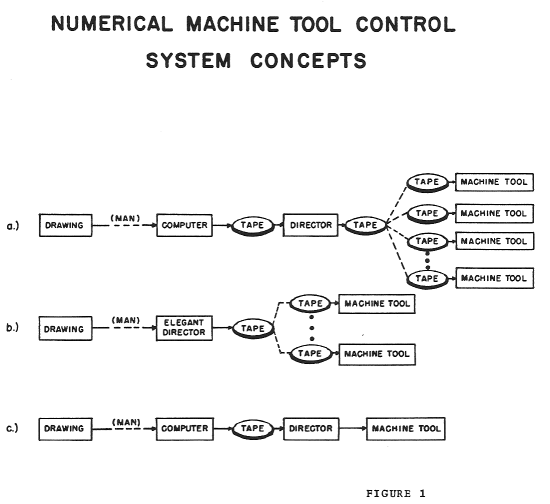
|
2. Enlarge versatility and capability of
basic machine tools
3. Perform Jobs otherwise impossible to do
4. Simplify, speed up, and reduce the expense of the overall manufacturing
operation.
There exist many philosophical approaches to solutions for these seven
objectives. The solutions vary depending on the machine tool application
(Figure 1). For production work, one system concept leads to the block
diagram solution shown as Product A. This solution is based on the fact
that the manufacturer has a large general purpose computer at his
disposal. It further assumes that this computer is to be employed for work
other than preparing machine tool data. With the tape intermediary between
the director and the machine tool, it is possible to split the cost of one
tape preparation device (director) among several
machine tools.
Product B shows a system concept applicable to manufacturers who do not
have a large computer at their disposal. The computer performs
automatically, all such operations as tool offset, interpolation, and the
vector resolution of cutting speed. The reasons for using an elegant
director instead of a general purpose computer are primarily economic. The
initial cost of the director should be lower than the initial cost of a
general purpose computer. Furthermore, this director should be capable of
preparing data for several machines at a much faster rate than a general
purpose computer can do it. Perhaps the greatest advantage of having this
special purpose director here is that it requires absolutely no
programming. One of the largest costs and the most time consuming
operation involved in running a general purpose computer is the
programming of the computer. With the elegant director, all operational
costs are minimized without limiting the generic types of machining
operations available to the manufacturer. It is not necessary to maintain
a mathematician to program the computer every time a new part is to
be machined ..
The third system approach to the machining problem is Shown as Product
C. This approach is useful and more economic to manufacturers who have a
limited number of machine tools they wish to control numerically. Here the
director is attached directly to a machine tool. Either the services of a
computer may be purchased when needed, or a small special purpose (or
general purpose, if desired) computer can be obtained for direct
utilization. This third scheme does lead to the ability to perform some
elegant machine tool control operations not otherwise available in the
first two systems concepts.
Now let us consider Linear Programming for Operation Research or
shall we say, the use of scientific management methods and devices.
Let us first ask some questions and then in turn answer these
questions:
What is Linear Programming? It's a mathematical technique for finding
an optimum solution to sets of simultaneous equations with more variables
than equations where the variables cannot have negative values. Or, in
common terms - Linear Programming provides a technique whereby the most
economical course may be computed and applied automatically.
53.
|
In what areas is Linear Programming
useful? Generally in the engineering planning and management decision
field; specifically, where the most profitable course of action (program)
must be chosen out of a number of' technically acceptable but less
profitable programs.
Why is Linear Programming important? Linear programming provides a
technique whereby the most economical course may be computed and applied
automatically, primarily, because it operates best in a field of paramount
importance to industry; optimizing profits. Where the technique is
applicable, it can find the one most profitable course of action among a
sea of possibilities.
Computers are rapidly coming into their own as vital tools for the
fledgling science of Operations Research. With the amount of computation
that must be performed on large operations research problems, electronic
computers are the obvious answer. Their speed, coupled with virtual
elimination of computation errors, 1I1akes them extremely attractive.
Operations Research can sometimes produce new answers or viewpoints in
what were previously considered unsolvable are as.
The areas where Linear Programming are important to you are:
Financial Control
Process Control
Transportation Control (Warehouse -
Factory)
Production Planning
Better Cost Data
or you simulate a model of your entire operation.
We are, at the present time, working with several operating departments
on a contributing basis, as well-as on a direct end-use product basis.
We believe that in surveying your requirements you will need and
must have specially designed computers for - Simulation - Process Control
- Machine Control - Special Purpose Control.
Since it is out charter responsibility it will, therefore, be our
continuing and willing desire to work with all of you on a cooperative and
effective approach for your specific computer needs.
WE ARE AT YOUR SERVICE --- USE US.
54·
|
BACK
TO INDEX OF SPEECHES |
|
|
|
|
|