Instruction Manual for Houston-Fearless PD-3 / RCA
Pedestal
http://www.smecc.org/media/rca-tv/Houston-Fearless-PD-3.pdf Do
not attempt to work on this by yourself, have several strong friends with
you.
History of Huston Fearless Keyword and
date and link to a more in-depth presentation - Mpe HF GROUP, INC.
THE RICH HISTORY OF HF GROUP, INC. (aka HOUSTON FEARLESS 76)
From http://hf76.com/about_us.asp
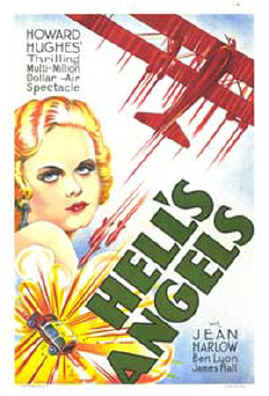
Houston Fearless 76, Inc., is a high technology firm engaged in the design, manufacturing and support of commercial equipment, including Film Processors, Cameras, Duplicators, Scanners, Advanced Oxidation/UV, Low Temperature Distillation systems and accessories. Our customer base includes the U.S. Government, private industry, and the international market. The company has provided several types of equipment and support services to the Air Force and other branches of the military. An operational support contract at Beale AFB has been held for over 30 years. Our ability to retain support contracts for so long is a testimony to our attention to customer service, superior personnel training, retention and satisfaction, and our ability to perform within the prescribed cost levels...
It all began in 1920 in Houston, Texas. H.W. “Hub” Houston was working for the Hughes Tool Company in the Research department directly with Howard Hughes on his dream of developing a steam automobile.
The following year, both young Texans, Howard Hughes and Hub Houston, set out for Los Angeles, California. With the intent of manufacturing those steam cars, they formed the Hughes Development Company with Hub as General Manager. They had brought a model of Hughes' steam car to Los Angeles for testing, demonstration and to further the development, but Howard became enamored in the motion picture industry, effectively halting the development of the steam car.
By 1926 Hughes had produced his first silent movie "Hell's Angels", but by the time it was ready for release, the first sound picture, "Wings", was already out. Hughes decided “Hell's Angels" needed sound and this required the design and production of special cameras, film processing and sound recording equipment. Hughes turned to his partner Hub at the Hughes Development Company.
By 1930, Hub, a brilliant engineer, had focused his entire attention on the new, rapidly growing industry of motion pictures and film processing. The flamboyant Hughes naturally gravitated towards the alluring pull of Hollywood movie stars and swimming pools and gave the film equipment end of the business to Hub. In 1936, Hughes helped Hub form the Houston Development Company, located in an old Hollywood building. They were dedicated to developing and refining the equipment used in motion picture film production.
By the late 1930's the Houston Development Company had designed and built much of the equipment used in the new Multicolor process (for Multicolor Corporation, which later became Color Corporation of America). In addition they built continuous film processors, as well as optical equipment and other photographic accessories for the Government and commercial use.
The early 194O's saw the on-set of World War II and the Houston Company moved from its cramped Hollywood headquarters to an isolated spot at the end of Olympic Boulevard in Los Angeles. The main building was erected in the middle of a bean field. The company began developing film for the war department and the first Houston Color Film Laboratory was established and located in part of the new building. There was a great demand for color film during the war and while its use grew there were not enough processors to keep up with the increasing demand. So, with the encouragement and funding from the Air Force, two portable continuous film processors were designed and built, one for 35mm and one for 16mm film.
Also during the war, in a small Culver City factory at a company called the Fearless Camera Company, a group of men were working on developing motion picture cameras and dollies to facilitate the modem director's desire for moving camera shots, prior to the forties, movies were shot with fixed camera locations and the action was directed around the camera location.
In 1950, the Houston Corporation of Los Angeles and Fearless Camera Company of Culver City merged to become the Houston Fearless Corporation. They became the first to make motion picture film processors, camera dollies and other equipment essential to television and motion picture production available to the entire entertainment industry. Through the ensuing years, Houston Fearless became the acknowledged leader in development of film processors and supporting equipment for the motion picture industry as well as for the rapidly expanding photo finishing and microfilm markets.
Since the beginning the companies emphasis had been on engineering excellence, the highest quality equipment, ease of use, and low maintenance. In time, the Houston Fearless name became indelibly imprinted in the historical annals of the motion picture and television industry... as well as on all its equipment.
As an innovative leader in the design and manufacture of equipment, Houston Fearless introduced products with unique modular designs, all stainless steel construction and features providing customized products without the custom design costs, unparalleled longevity of service and ease of maintenance. This attention to design and detail led to Houston Fearless becoming the undisputed leader in the film processing market.
1964, during the height of cold war, Houston Fearless became involved in the SR-71 Blackbird and U-2 spy plane programs by supplying high speed photo processing equipment to the US Air Force. For the rest of the 1960's, Houston Fearless' participation in the SR-71 program gradually increased until the special operations onsite staff grew to around 100 employees. Their mission; to support the Air Force worldwide, with specialized equipment and engineering services.
In 1971 Houston Fearless was purchased by ATI Corporation of Dayton, Ohio, and became known as "Technology Incorporated, HF Photo Systems Division". During this time HF Photo Systems continued to be the undisputed leader with many new innovative products. Responding to customers needs, HF Photo Systems manufactured the most precision engineered line of duplicators and cutters available in the microfilm world. In line with their history, the products reflected the dependable reliability firmly associated with the Houston Fearless name. HF Photo Systems also developed a new method of silver recovery with a process that recoups dissolved silver from used photo fixer solution before it is disposed of.
Then in 1976 the HF Photo systems division was spun off from ATI and was purchased by M.S. Lee and D. J. Macho to form Houston Fearless 76, Incorporated. Co-founders Lee and Macho dramatically expanded the company's product lines to include a complete family of both color and black and white film processors, which handled every film process and every film size.
In 1989 the SR71 Blackbird program was shut down and Houston Fearless moved over their operation to support the U2 program. Houston Fearless' team of engineers and technicians having highly refined capabilities and the facilities to support mobile shelter programs, ground support equipment (GSE), environmental control units (ECU), power generation and distribution systems, film processing, digital imaging, emergency field repair, depot-level overhaul and remanufacture, were deemed too strategically important to the Air Force. Keeping strategic or tactical operations running smoothly around the clock with configuration control, spares provisioning and cataloging, technical data and training, field engineering, and contract field service (CFS) are additional strengths that made sense to the Air Force during the transition.
1982, saw the beginning of an ambitious growth program through acquisitions, between 1982 and 2003 Houston Fearless purchased and sold a variety of film based and digital imaging companies including; Oscar Fisher Corporation of New York, a company that produced equipment for the graphics art community: Extek Microsystems of Van Nuys, California, a film duplicator equipment manufacturer: Houston International, a former division of Houston Fearless, still run by the sons of former owner Hub Houston, manufacturing consumer photo processing equipment in Yuma Arizona: Mekel Engineering of Brea California, a microfilm digitizing equipment manufacturer: and Ascendant Solutions International, the US Marketing arm for FUJI Photo Film Corporation.
In the late 80's, the US government was becoming increasingly sensitive to waste streams that it was generating. The EPA took action against the U-2 photo-processing lab by issuing a cease and desist order against its waste stream in 1989. At that time, up to 88,000 gallons of highly contaminated photographic waste and wastewater were being routed to the base treatment facility daily.
Bold thinking by several Air Force personnel, led by Michael Freiberg who felt that the only acceptable solution would be to completely eliminate the waste stream focused on the holy grail of environmental engineering, the 'true zero discharge' system was about to be born. The Air Force quickly capitalized on promising research originating from the Department of Energy. Houston Fearless personnel were intimately associated with the development of the Advanced Oxidation and Low Temperature Distillation systems, receiving design patents for their contributions to the project while working alongside the Air Force concept development team.
The idea was not only intended to remove the Cease and Desist order, but also to cause the EPA to lose interest in the U-2 Air Force Base photo lab. Ultimately the systems developed enabled the Houston Fearless team to literally cement the drains shut!
The pollution control system that was designed for the U-2 Air Force Base photo lab consisted of a Houston Fearless designed and built Vacuum Distillation system, an Advanced Oxidation unit and a Reverse Osmosis membrane. Distillation removes all undissolved solids in the waste stream, producing a pumpable sludge concentrate representing approximately 3% of the original waste stream, and water (the distillate). In the second step of the process, the distillate is further refined through polishing. By processing through a Reverse Osmosis membrane, dissolved chemicals are separated out. Next, Advanced Oxidation utilizes Ozone and UV light to destroy any remaining organics, and finally a deionization system completes the process. This ultra pure water is sent back to the lab again for reuse. Additional processes designed by Houston Fearless engineers include, pH control, carbon and particulate filtration, 03 and nitrogen infusion, and electrolytic silver recovery.
The Air Force photo lab Pollution Control System reduced an 88,000 gallon per day hazardous waste stream to approximately 22 gallons per day of concentrated sludge which is collected and recycled. The lab continues to use its recycled water and has done so for more than ten years. A year later the California EPA removed the Cease and Desist order and classified the lab as a recycling process exempt from permitting.
In 1992 M.S. Lee became the sole private owner of Houston Fearless 76, Inc. At the same time the looming digital imaging industry was threatening most of the Houston Fearless film based business. The company pursued a strategy of becoming the industry leader in each of their declining markets while continuing to expand their Pollution Control Systems capability. Initially by selling to other military and government installations that were doing film processing both here and abroad, Houston Fearless was able to further refine the design and capability of their equipment.
Throughout the 90's Houston Fearless Special Projects Group Engineers continued to design and manufacture a wide range of mobile systems for the U.S. Air Force, including Mobile Shelters and Complexes, Mobile Power Generation and Distribution Systems.
In 2003 the company has its own research and development, design, engineering, manufacturing, testing, and service facilities, staffed with a highly skilled workforce producing a range of standard products, customized systems and engineering services. Squarely focused on commercialization of their technology, Houston Fearless is once again poised to be a world leader in the rapidly expanding drinking water safety and commercial wastewater treatment markets. Employees of the Houston Fearless organization are very proud of our history and the success the company has achieved. They are dedicated to continuing the quality of service, innovative thinking and delivery of products that has fulfilled our customer's highest expectations. The future of Houston Fearless will be influenced by the value we place in honoring our tradition and by continuing to solve our customers most difficult environmental issues.
|
RCA Tripods, Pedestals, Cranes and
Dollies
RCA /Houston Fearless Panoram Dolly
TD-5A
Perhaps the HF part # is PD-1-A
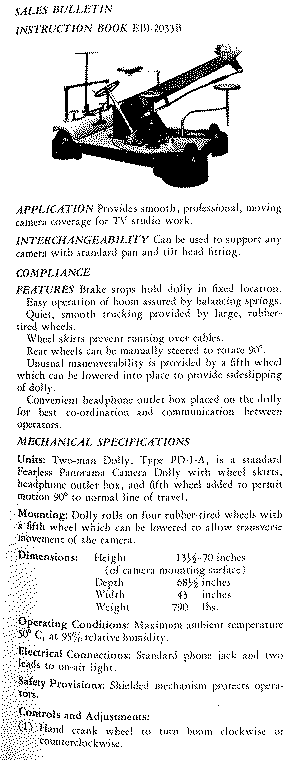
|
RCA /Houston Fearless Panoram Dolly
TD-5A
Control Identification and
operation from Broadcast Equipment Data Book - October 1, 1950 This is
Sales Bulletin Instruction Book EBI-2033B
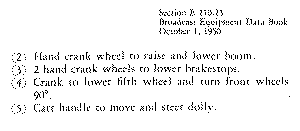
|
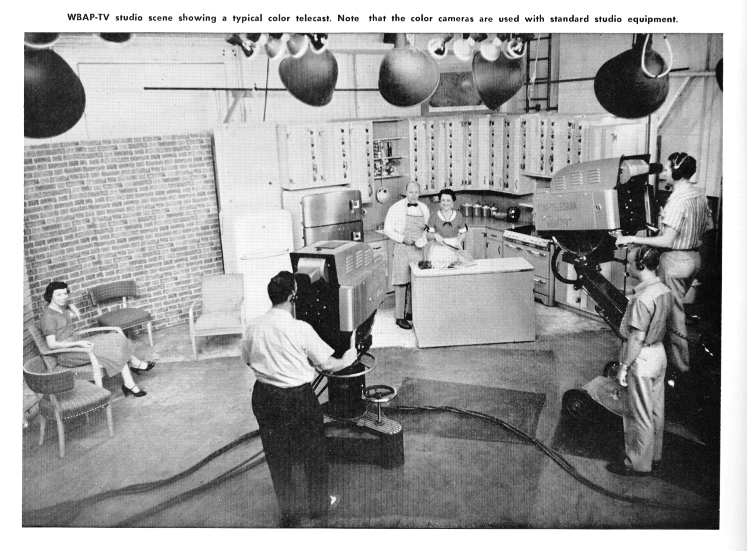
WBAP-TV studio scene showing a typical color telecast. Note
that the color cameras are used with standard studio equipment.
TV CAMERAS
Removing the viewfinder also gives access to the plug-in preamplifiers
located just ahead of the top shelf. These supply the red, blue and green
signals to the camera cables and the camera viewfinder. Each of the
preamplifiers includes six stages. The first four are simple shuntpeaked
stages. The second stage has a screwdriver adjusted cathode peaking
circuit for adjusting tilt in the low-frequency end of the response curve
of the amplifiers. In the cathode of the third stage there is a similar
circuit with a knob type control which may be adjusted to give minimum
streaking for the associated image orthicon. The last two stages are a
feed-back pair, providing cathode output to the 51-ohm camera cables and
to the viewfinder. There is an adjustable trimmer in this stage which
affects the response curve tilt at the high-frequency end. Each of the
preamplifiers is shock mounted and bonded to the cross members of the
upper camera framing.
Two tally lights are mounted on the front face of the camera. They
serve to indicate to the actors when the camera is in actual use. In
addition, there is one on top of the viewfinder for directors and one on
the kinescope bezel plate for the operator. The latter are operative,
however, only when used in conjunction with a camera switching unit. The
lights are normally off until a tally relay is actuated by a control
voltage (24 volts d-c).
The individual image orthicon tubes and the area within the camera
housing are forced-air cooled. Separate blowers are used to cool the
individual image orthicon tubes. Cooling air is brought into the socket
end of each yoke assembly by means of flexible hose leading from its
associated blower. All external areas of the camera and viewfinder have an
aluminum finish to further aid in maintaining optimum temperature
conditions within the camera. Two utility outlets and a fuse are mounted
on the under side at the back end of the camera. They provide facilities
for an independent source of a-c that may be used for test equipment.
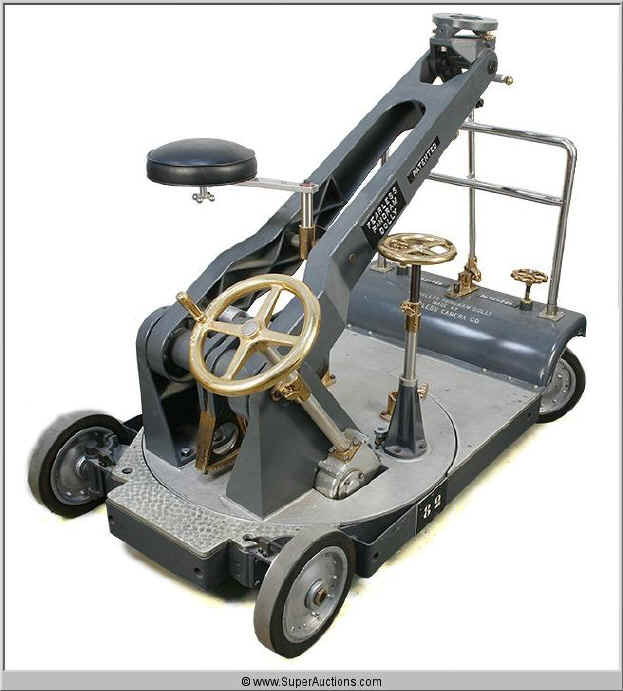
An
extremely 'Pimped out' Panoram in a Hollywood auction...
http://www.icollector.com/Fearless-Panoram-Camera-Dolly_i8757900
Hollywood Early Dolly History -
Camera Movement.
Great article - keywords... go to the link for the
complete article!
History on: Bell & Howell
Rotambulator, introduced in 1932. The Fox Velocilator (introduced
in 1933 and manufactured by the Fearless Camera Company). The
Fearless Company’s Panoram Dolly, which debuted in 1936.
The Velocilator appears to have
been the basis of Erik Charell’s CARAVAN (FOX,
1934);
Tracking movements that followed
the movements of the players, as in the CHARGE
OF THE LIGHT BRIGADE
The new dollies made feasible the
sort of tight, minute adjustments of framing seen in the LIGHT
BRIGADE sequence.
The enormous Universal camera crane used
on BROADWAY (1929), with its
twenty-five-foot-long arm, had represented the summit of such efforts at
the end of the silent era. The small sets in early talkies did not favor
such equipment, but after 1931, cranes were proving feasible again. The BROADWAY
behemoth was trundled out for ALL QUIET
ON THE WESTERN FRONT
(1930), and MGM and UA also began using
cranes. In 1932, at an Academy equipment demonstration,
Paramount displayed its “Baby” camera boom, which could rise from
floor level to a height of about eight feet.
A 1931 article pointed out that
filming from a moving crane yielded fluidity and spectacle.
John Arnold’s MGM
boom, introduced in 1939
Crane shots are a major attraction of the
musical numbers in such Busby Berkeley films as FOOTLIGHT
PARADE (1933) and GOLD
DIGGERS OF 1933. Stately crane movements are
particularly in evidence in MGM’s THE WIZARD
OF OZ (1939) and GONE WITH
THE WIND
(1939).
Read more: Technological
Change and Classical Film Style - A Specimen Scene, THE CHARGE OF THE
LIGHT BRIGADE Scene 34, Sources of Innovation, Case Studies http://encyclopedia.jrank.org/articles/pages/2888/Technological-Change-and-Classical-Film-Style.html#ixzz1XRK5NcaN
We are looking for more photos,
history articles and reminisces - Email us at info@smecc.org
RCA TD3-A Pedestal (Actually a Houston-Fearless
PD-3)
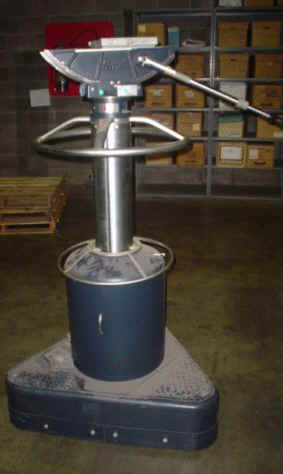 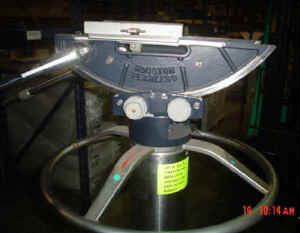
|